Case Study
Case Study
01
01
01
Cyclone Underflow Pipes
Cyclone Underflow Pipes
Cyclone Underflow Pipes
Extreme Cost-Effectiveness with 7 Times the Wear Life of Traditional Lined Piping
Extreme Cost-Effectiveness with 7 Times the Wear Life of Traditional Lined Piping
Extreme Cost-Effectiveness with 7 Times the Wear Life of Traditional Lined Piping
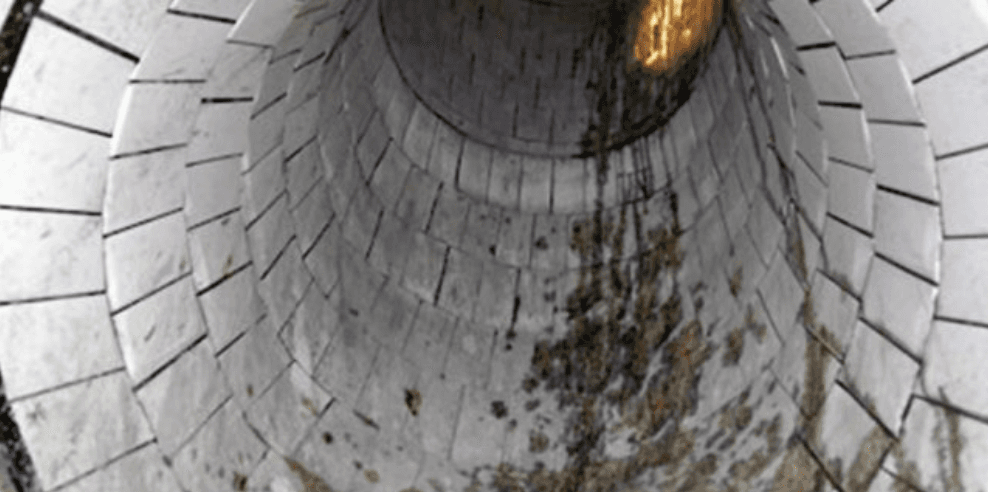
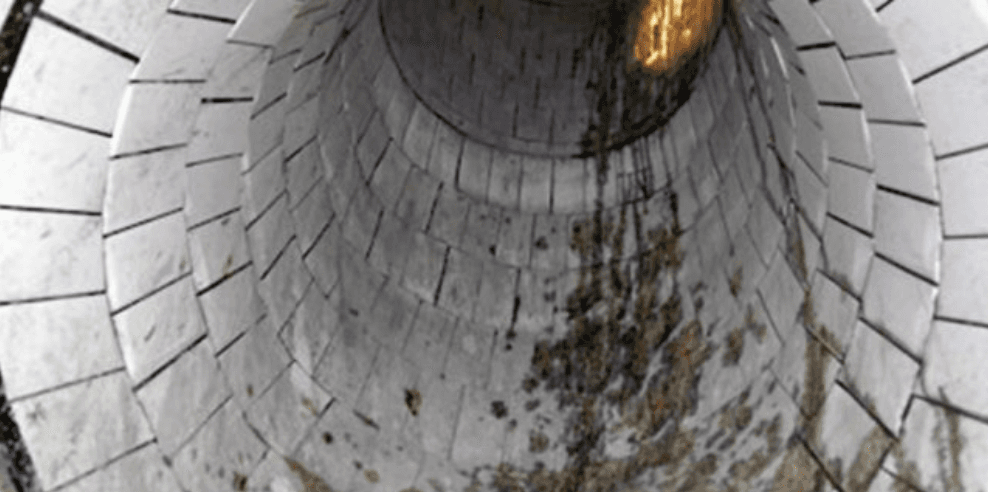
Details
Details
Details
Product
Product
Ceramic Liner
Ceramic Liner
Material Handled
Material Handled
Gold Ore
Gold Ore
Tonnage
Tonnage
Particle Size
Particle Size
<19mm
<19mm
Location
Location
Australia
Australia
Application
Application
Distributor to Ball Mill - Piping
Distributor to Ball Mill - Piping
Material Handled
Gold Ore
Tonnage
Particle Size
<19mm
Location
Australia
Application
Distributor to Ball Mill - Piping
Images
Images
Images
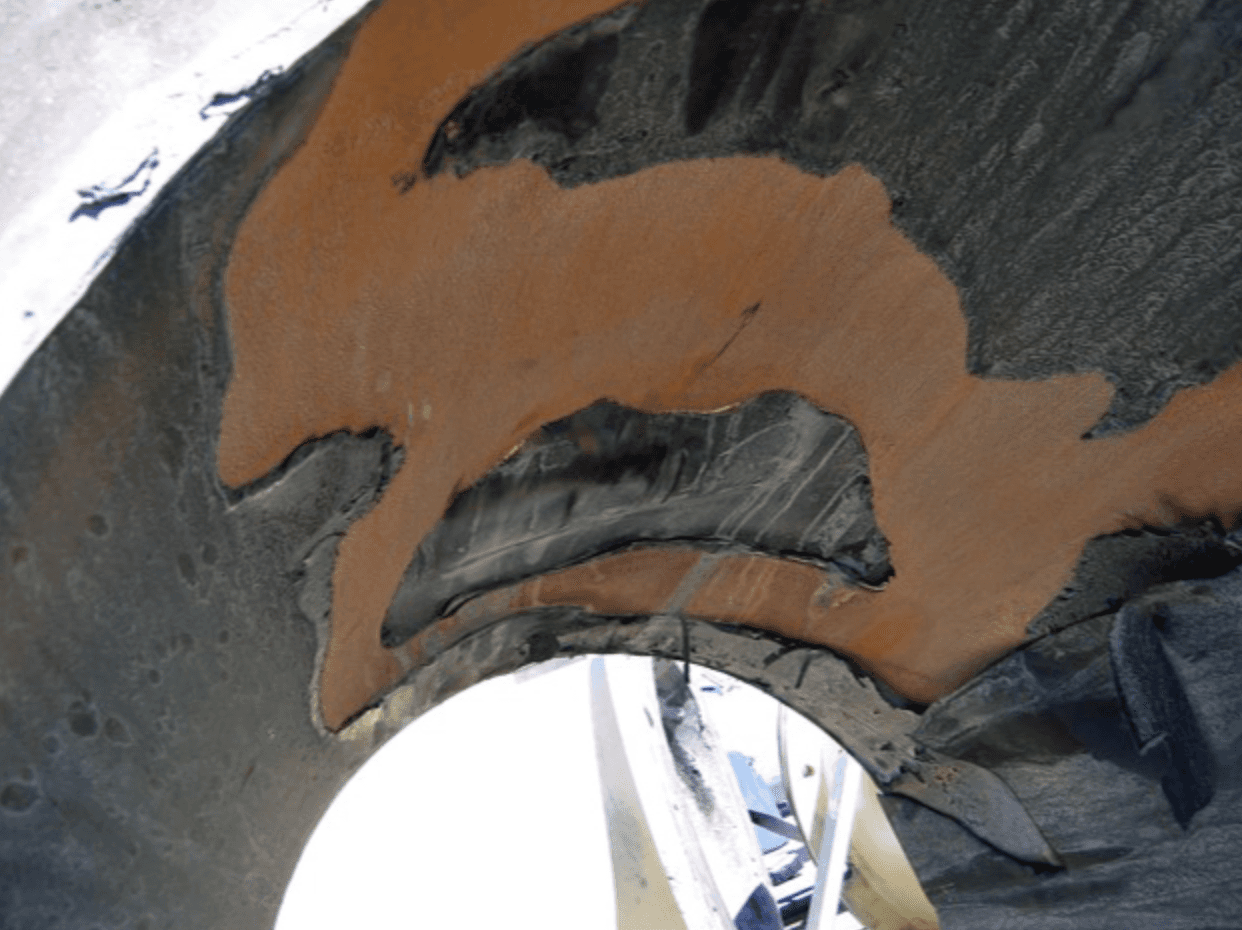
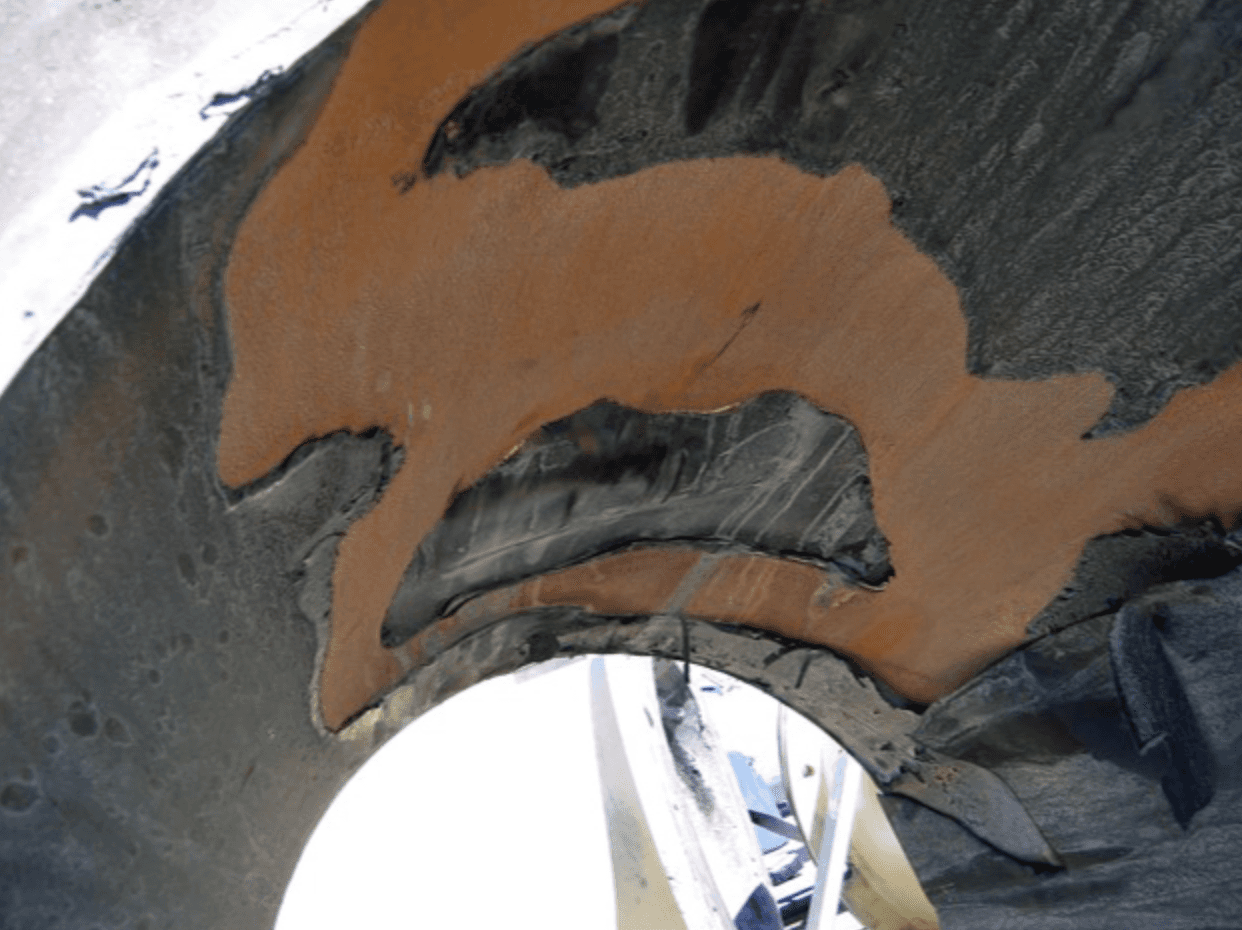
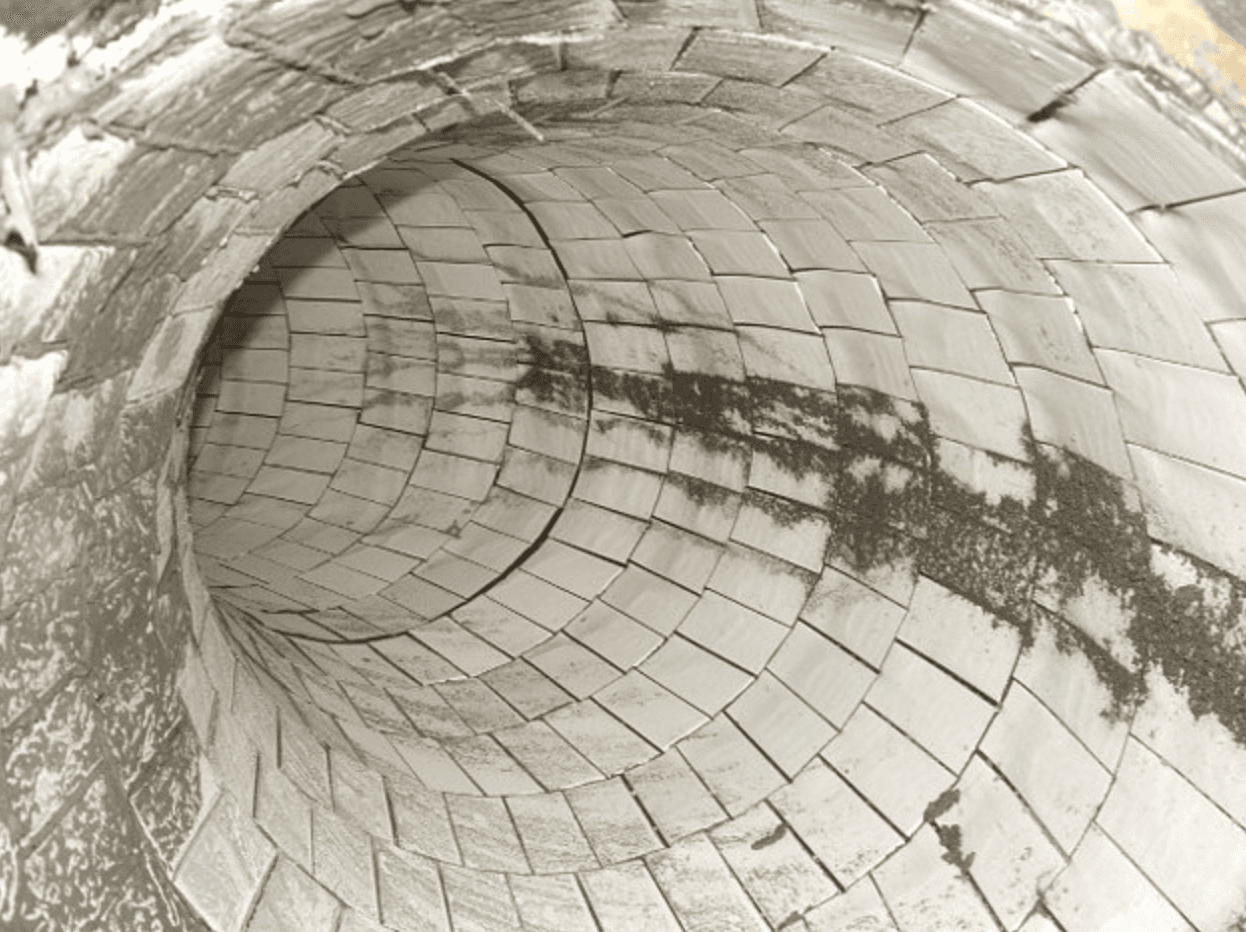
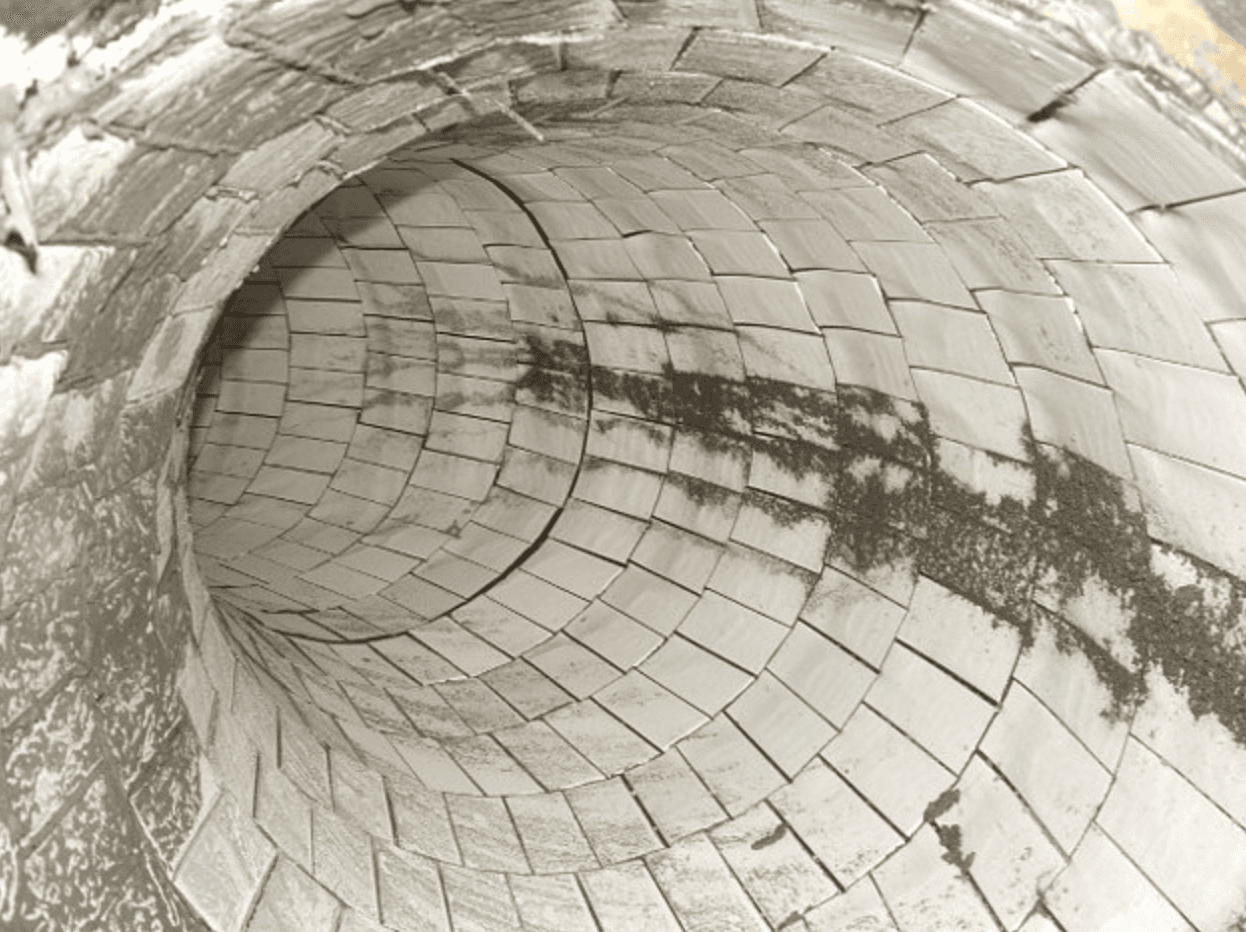
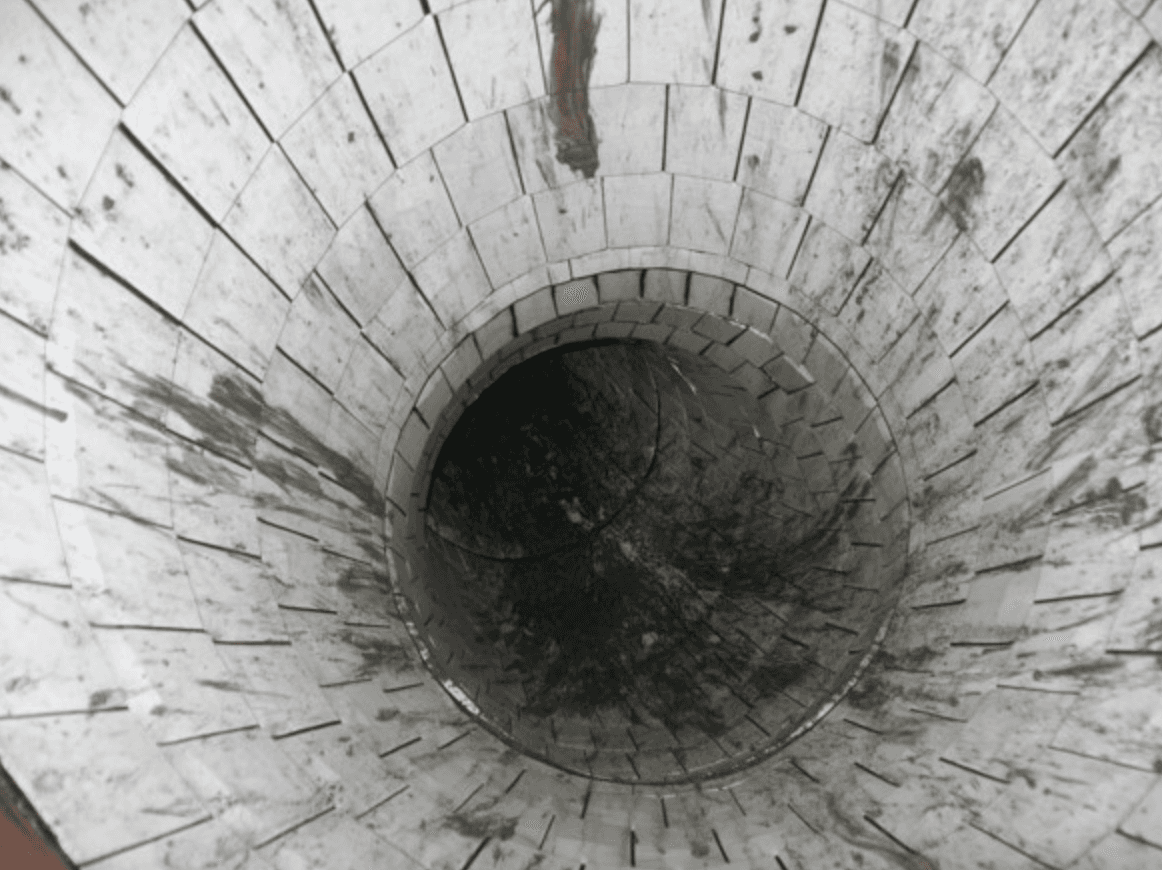
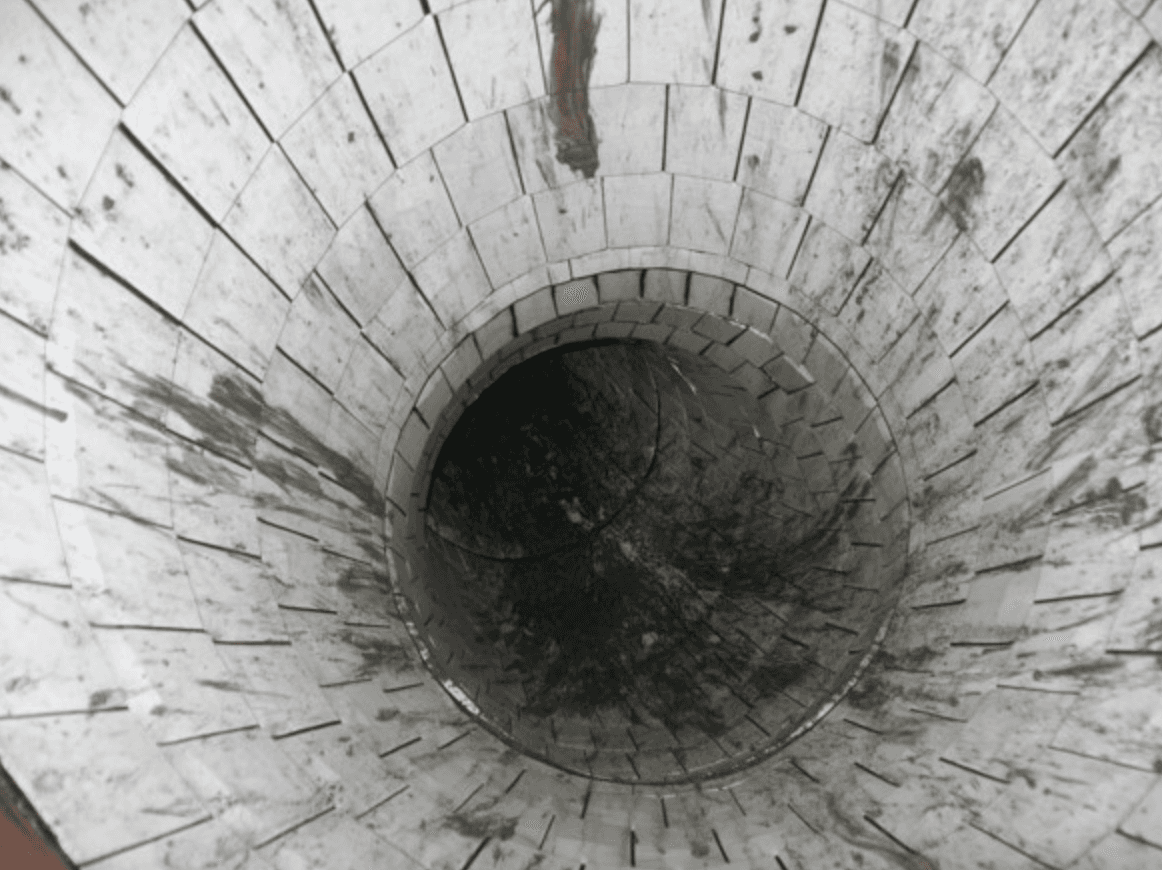
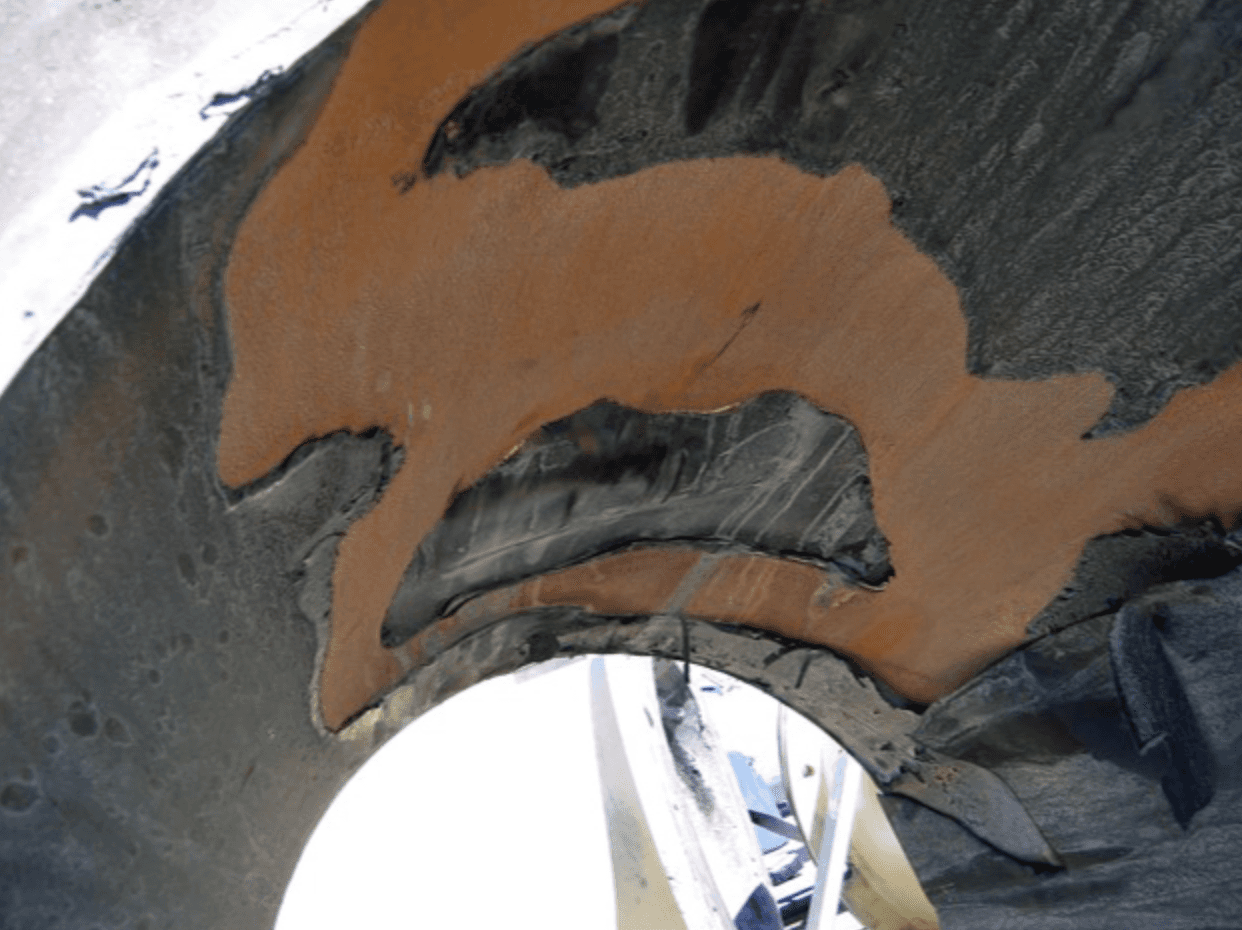
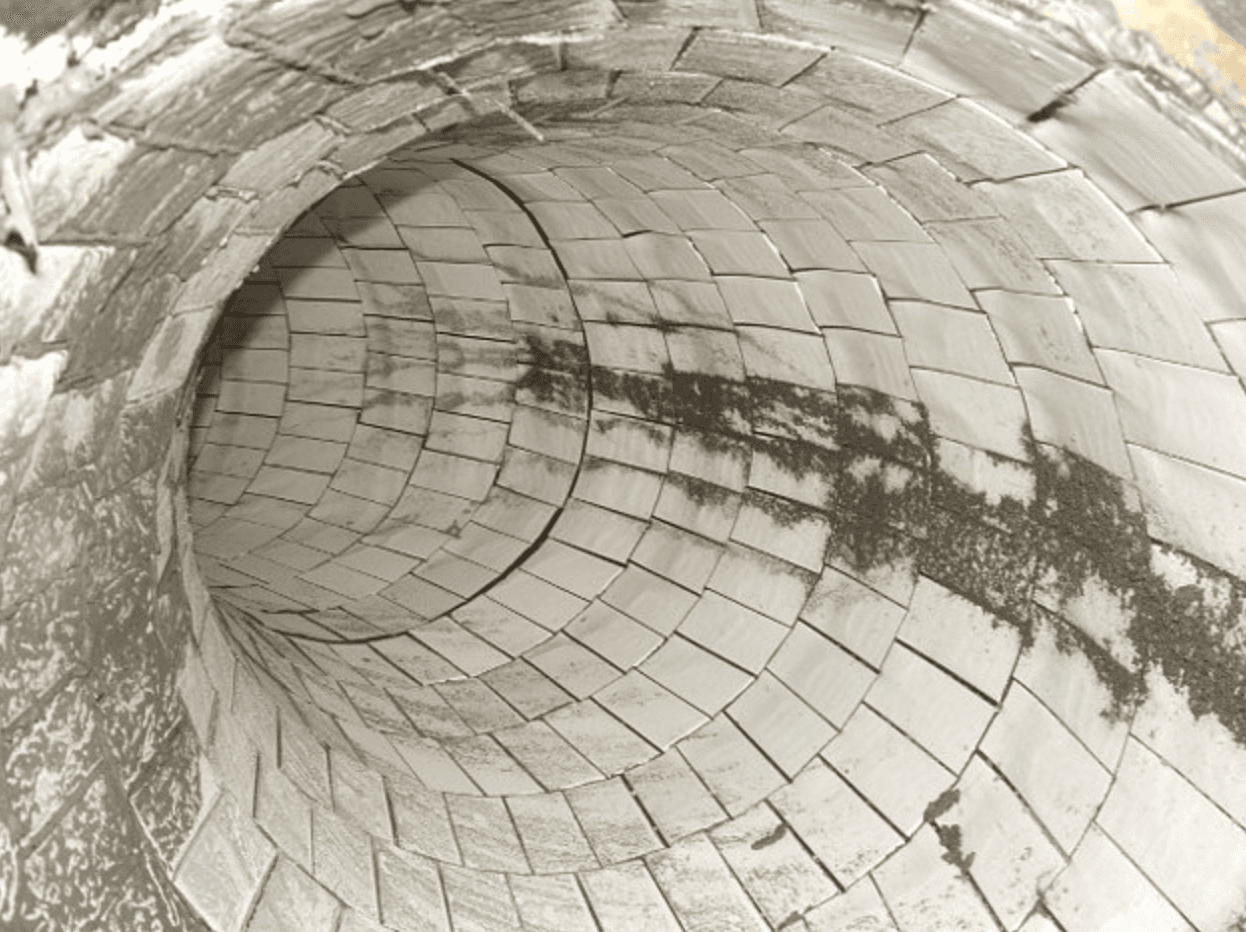
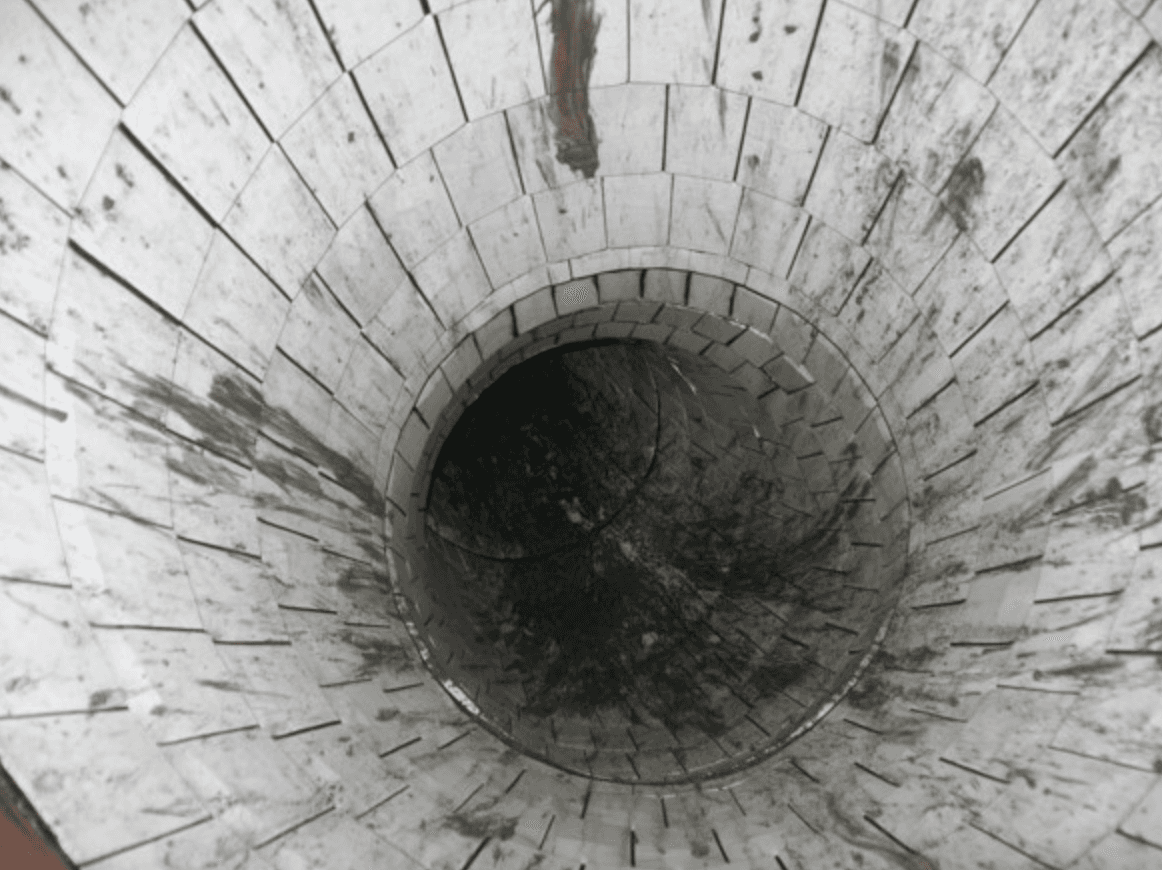
Challenges
Challenges
Challenges
The previous rubber lining wear material needed to be replaced every 13 weeks (lasting only 1 shutdown interval). This was unsatisfactory for the client, who also tried a Ni-Hard wear lining, lasting just 22 weeks. With the highly abrasive material, a next-generation solution needed to be engineered for this pipe to last longer without the need of unscheduled downtime.
The previous rubber lining wear material needed to be replaced every 13 weeks (lasting only 1 shutdown interval). This was unsatisfactory for the client, who also tried a Ni-Hard wear lining, lasting just 22 weeks. With the highly abrasive material, a next-generation solution needed to be engineered for this pipe to last longer without the need of unscheduled downtime.
Solutions
Solutions
Solutions
Corrosion Engineering custom-designed and engineered a rubber and ceramic lining to be installed in the pipe with engineered ceramic tile segments bonded in rubber. This lining would be powerful against severe abrasion, wear and chemical attack.
Corrosion Engineering custom-designed and engineered a rubber and ceramic lining to be installed in the pipe with engineered ceramic tile segments bonded in rubber. This lining would be powerful against severe abrasion, wear and chemical attack.
Results
Results
Results
The initial engineered ceramic system was in service for over 78 weeks (lasting over 6 shutdown intervals). Wear studies were conducted and measurements taken from the used pipes indicated that they could've lasted another shutdown, if required.
Conclusion
Conclusion
Conclusion
At present, the replacements are scheduled to occur every 7 shutdowns (91 weeks). This long-lasting solution has proved to be highly cost-effective, with conservative payback at 5 shutdowns and dramatic savings from highly reduced hazardous maintenance.
At present, the replacements are scheduled to occur every 7 shutdowns (91 weeks). This long-lasting solution has proved to be highly cost-effective, with conservative payback at 5 shutdowns and dramatic savings from highly reduced hazardous maintenance.
ready to get started?
Sign up for our Newsletter
ready to
get started?
Sign up for our Newsletter
© Copyright 2024 Corrosion Engineering